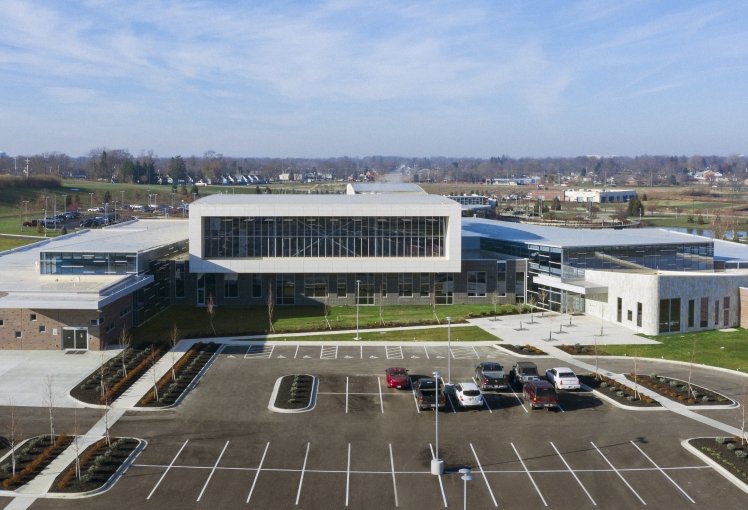
Community Tissue Service's Center for Tissue Innovation and Research (CTIR) located in Kettering, Ohio, is one of the world's premier manufacturing facilities of skin grafts, bone grafts, dental implants and other surgical parts fabricated from tissue donors. Shook Construction had previously completed Phase I of CTIR in 2011, a new 94,000 SF facility that included research laboratories, office space and 14 cleanroom production suites. Due to immense growth, CTIR was working three shifts a day and needed additional space for expansion. Given our success on the Phase I project, Shook was selected as the Construction Manager at Risk for their Phase II expansion, which included a $50 Million, 132,000-square-foot addition of a bio-medical manufacturing facility with 16 ISO Class 5 Cleanrooms, a generator building with three 2.5-megawatt diesel generators, 25-acres of site work, and a new utility plant with connections that fed back into the original 95,000-square-foot manufacturing facility. Additionally, the new facility includes 18 new conference rooms, open collaboration spaces, executive offices, and a 40% larger central sterilization space to sustain the cleanroom workflow.
The 17,000 SF mezzanine houses 26 air handlers providing 500 air changes per hour in the cleanrooms. The cleanroom ceiling system, comprised of 100% HEPA filters, prevents contamination in the manufacturing process. Each cleanroom suite has four stainless steel-clad sliding doors which create the necessary airlock preventing cross-contamination airflow. The new central plant provides redundant chilled water, higher quality steam, reverse osmosis pure water and backup generators which were all fed back into the existing Phase 1 production facility without impacting existing operations. Each system was deliberately designed to prevent a single point of failure to minimize downtime.
The project broke ground in November ahead of a wet winter. Shook’s project team analyzed the work scheduled and developed a plan to use cement to stabilize the 132,000 SF building pad. Though costly, the underslab plumbing, footings and other deep utility work would not destroy the building pad in preparation for slabs and steel erection. Concrete trucks and excavators easily ran over the stabilized pad adequate to hold their weight. This added work proved to be one of the team’s smartest decisions early in the job as it helped drive the schedule.
Additionally, the 26 air handlers were produced in Canada and had engineers’ specifications stating they could not be stored outside. Our planning and coordination required equipment manufacturers, hauling contractors, riggers, and the concrete team to ensure the equipment would not be exposed to the elements. To overcome this unique challenge, AHUs were delivered through customs in a specific sequence, loaded onto the mezzanine through the building’s open curtain wall and placed from back to front. An hourly timeline was built to schedule arrival times and facilitate delivery, rigging, placement and subsequent equipment pad pours to achieve certainty of results.
Five major utility connections were needed to tie into the existing 95,000 SF facility. These included sanitary lines with a new fat oil and grease separator, high-pressure steam for sterilization equipment, reverse osmosis pure water, chilled water, and most challenging electrical from the new generator facility. In order to avoid a complete shutdown of the facility, Shook detailed a shutdown schedule with each trade identifying key constraints and deliverables. Our crews completed the work on Saturday nights after 8:00 PM with all shutdown work being completed by Sunday night at 11:00 PM when third shift manufacturing started their day. The most challenging of the chilled water connections were made on Thanksgiving and Black Friday when the facility was closed to avoid impact to CTIR’s operations.
Shook encouraged our trade partners to utilize prefabrication efforts to drive the schedule. The metal stud contractor panelized their exterior framing in order to improve the efficiency and safety of the building skin installation. Apprentices assembled metal stud panels off-site in their shop and then brought the panels on site and installed them en masse. The result was a speedy installation, which allowed us to begin the installation of masonry immediately following the start of this activity. Our electricians also saved time with diligent prefabrication efforts. They were able to significantly shorten their time doing in-wall rough-in by tasking apprentices with pre-assembly. The electricians went through the entire set of drawings and determined what components were needed in each room such as outlets, switches, and pull boxes. Each of these components were then sorted and placed in boxes labeled with the appropriate room number. With the majority of the necessary material located in the appropriate rooms, it nearly halved the duration of in-wall rough-ins.
3D model coordination was more critical than ever on the CTIR project as the complexity of the 16 air handling units, associated ductwork, electrical conduit, plumbing, mechanical piping, and compressed air lines ensured that there would be no wasted space above the cleanrooms. By catching conflicts early, we reduced the cost of changes and rework. In the process of coordinating the clean core area, we caught an issue that, if ignored until the construction phase, could have spelled disaster. Running clash detection between the structural steel model and the cleanroom model revealed to us that the cleanroom model was generated based on an outdated set of plans. The construction documents showed the steel beams in that area were rotated 90 degrees from their original position in the design documents. This early discovery as part of our regular BIM process allowed us the necessary time to design and procure the steel superstructure to support the walls and ceilings of the cleanrooms based on the new structural layout. Although there was a cost associated with this change, it mitigated what could have been a significant time and cost issue down the road. Realizing this error during the course of construction would have been a monumental blow to both schedule and morale.
The CTIR campus is unique in the industrial field in that it is both highly functional and architecturally stunning. Significant design innovation and construction efforts were necessary to achieve both the desired look and performance. The large office space in the northern half of the building required massive 96”x46” ductwork to keep the air moving. The duct was fed by air handlers in another part of the building, crossing a high-traffic hallway. To preserve the aesthetics of the space, this ductwork was designed to run underground and then raise back up in a chase. Out of an abundance of caution for mold and other contaminants to the air supply, we sealed the depression with a waterproofing epoxy product and installed a moisture meter to constantly monitor for leaks.
The cleanroom commissioning and validation was an intensive process. Because CTIR’s products are used for surgical procedures, their cleanliness and air quality standards are regulated by the FDA. To achieve successful validation, the clean core was “triple cleaned” to sterilize the space prior to air testing. Despite repeated cleanings, the return corridor in the new space continued to test positive for streptomyces, a non-harmful bacteria found in dirt. Shook worked to solve the problem by performing root cause analysis with stakeholders and developing a day-by-day remediation plan. During an investigation in the return corridor, we found swirling airflow instead of a cascading airflow. Our team realized the turbulence was being caused by an air gap under the sliding glass doors. Air sweeping across the floor from two opposite production suites would meet and force a column of air up into the space instead of remaining low to the ground and working to the return vents. The Shook team quickly fabricated stainless steel sweeps to fasten at the bottom to minimize the gap. Once the air gap was eliminated, the validation team tested and achieved FDA-certified results, allowing for the manufacturing of life-saving products to begin.