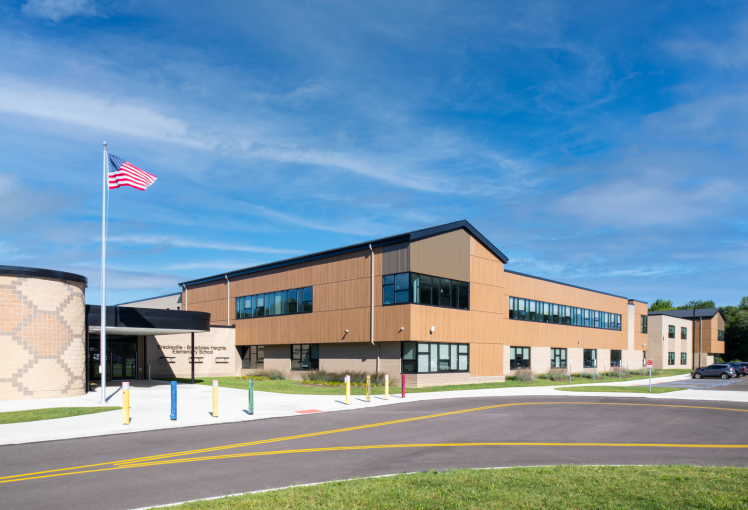
With costs of maintaining aging facilities increasing and enrollment decreasing, the Brecksville-Broadview Heights City School District needed updated, consolidated facilities to house their 4,000 students and improve educational offerings. Additionally, the City of Brecksville was seeking expanded recreation space to house athletic tournaments and community events. In 2018, the District issued a $44.5 million bond to fund various improvements, including consolidating four elementaries into one PK-5 building and renovating select areas of the middle and high schools. Through collaborative discussions and an agreement between the District and City, a jointly owned field house was added to the scope and integrated with the construction of the elementary. The agreement allowed the school to use the facilities during the day and the city to use them outside school hours.
The District selected Shook and ThenDesign Architecture to design and construct the new facilities. Meetings with District leaders, community members, and key stakeholders were conducted to shape the design and functionality of the new buildings, resulting in a 130,000 square-foot elementary and 30,000 square-foot field house. Unique features were incorporated throughout the school, including a stamped concrete courtyard with a functional pond and boardwalk, an interior corkscrew slide from the second floor to the media center, window alcove seats, and collaboration areas. Hexagonal shapes were also carried throughout the design in the windows and finishes to celebrate the school’s Bee mascot.
The field house, a pre-engineered metal building attached to the school, houses four basketball courts with a two-lane track around it and various reception, office, and storage areas. The gym offers multiple basketball configurations, adjustable nets/striping for volleyball and pickleball courts, full-height motorized divider curtains, and a batting cage.
The team executed this challenging project without incident, on schedule, and within budget during the height of COVID-19 and amidst unprecedented supply chain issues.
From the start of preconstruction, the project was challenged by a budget that was insufficient for the desired scope. Working in concert with the Owner and Design Team, Shook developed a series of Value Engineering items that significantly reduced cost without sacrificing critical programming in terms of square footage, quality or longevity. Under the guidance of the Shook BIM department, the mechanical trades reviewed piping and duct layout throughout the entire building. Areas of interference were identified and taken back to the design team, which allowed for wall and ceiling height adjustments prior to fabrication and installation. In total, nearly $3 Million in accepted Value Engineering was realized for the project. Examples include:
Exterior
Interior
This project required collaboration from the start, as the project had co-owners with shared scope. As an added layer of complexity and coordination, the City of Broadview Heights and the Cleveland Metroparks had a vested interest in the project. At the early onset, the team established key decision-makers to streamline the decision-making process. This approach, along with a collaborative culture, open communication, and honesty of the team allowed for quick decision-making, which kept the project on schedule.
As a result of having multiple owners occupying the building at different times, there was special consideration for managing the building automation system, tracking utility usage, and security. The processes and procedures for these systems were set up and agreed upon early on in the project which allowed the design and construction to proceed as scheduled.
Shook had to drive the project schedule in order to meet the project deadline in the midst of COVID-19 and long material lead times. As with all projects during this time period, the uncertainties of COVID-19 had major implications on the project. From the start, tree clearing in Northeast Ohio must contend with weather and Indiana bat restrictions; however, COVID added additional complications. The daily threat of being shut down by the state required our team to drop trees in an unorganized fashion to ensure all required areas were on the ground before we reached the cutting deadline. This increased the way material was moved and stockpiled prior to leaving the site, and slowed our ability to start the mass excavation and fill until the site was clear. Furthermore, monitoring worker illness, documenting tardiness, spacing workers, and additional relief money added to the continued daily burden not typically seen on a construction site.
The lengthening of material lead times was also a large hurdle. Our team constantly kept this at the front of discussion and prioritized having subcontractors stay ahead of their discipline’s shortages. An unprecedented amount of time was spent to obtain all material needed on site, as well as coordinate and take delivery of the items to ensure they were available for installation. Despite these numerous barriers to the schedule, our team’s forward vision and planning allowed the project to be completed within the established timeframe.